Supervisor
Goals
Understand the role of the Supervisor.
Know how to complete Batch Sign Off.
Know how to generate and merge Batch reports.
Term | Definition |
Sign Off | Final review of a Batch. |
Signature Flow | Structured signature queues configured in L7|Master. |
L7 MES Tab | Activity | Permission(s) |
---|---|---|
Quality Review | Request changes to a Step | MES → Operations Review or MES → Quality Review and LIMS → Sample Sheet → Update |
Quality Review | Enter an Exception Assessment and push to QMS | MES → Quality Review LIMS → Sample Sheet → Update Analysis → Pipeline → Execute |
Sign Off | Sign a Signature Flow | Access to L7 MES |
Reports | Generate a report | Access to L7 MES |
Reports | Attach a report to the Batch | Access to L7 MES Data → File → Register |
Attachments | Attach a File | Access to L7 MES Data → File → Register |
The Supervisor is part of the final review and sign off of a Batch in L7 MES. They also save and export reports required for Batch disposition. To complete these tasks, they use all of the tabs within the Batch Record.
![]() |
The Sign Off tab provides a mechanism for final review of a Batch in L7 MES. Users with the appropriate permissions (see above) can request changes and triage exceptions up to the point that the final signature is entered.
Note
If changes are requested or assessments made, the Batch reverts to a "review" status and all Quality Review and Sign Off signatures must be entered again.
Sign Off signatures can only be entered after Quality Review has been completed.
The signatures presented in Sign Off tab are governed by the Signature Flow associated with the Batch Recipe. The signer does not have to be the logged-in user.
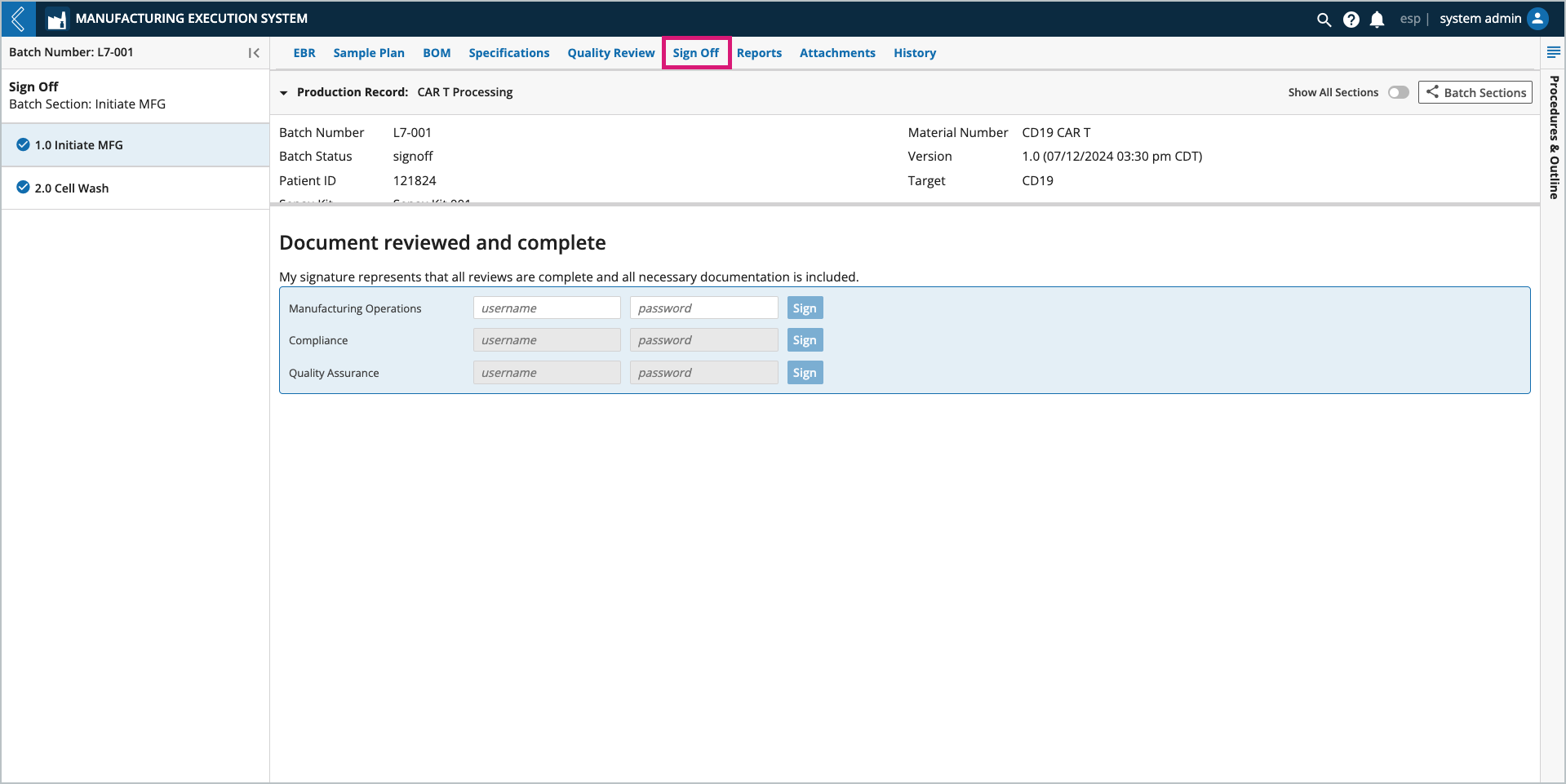
Once all signatures are entered, the Batch status is updated to Complete.
Note
Completed signatures record the reason, username, and date time of the signature, making them 21 CFR Part 11 compliant.
All reports, except the Master Batch Record and Transition Genealogy Report, observe the sort order for the Batch Sections. To change the sort order, select Execution Order or Numeric Order above the list of Batch Sections in the left panel.
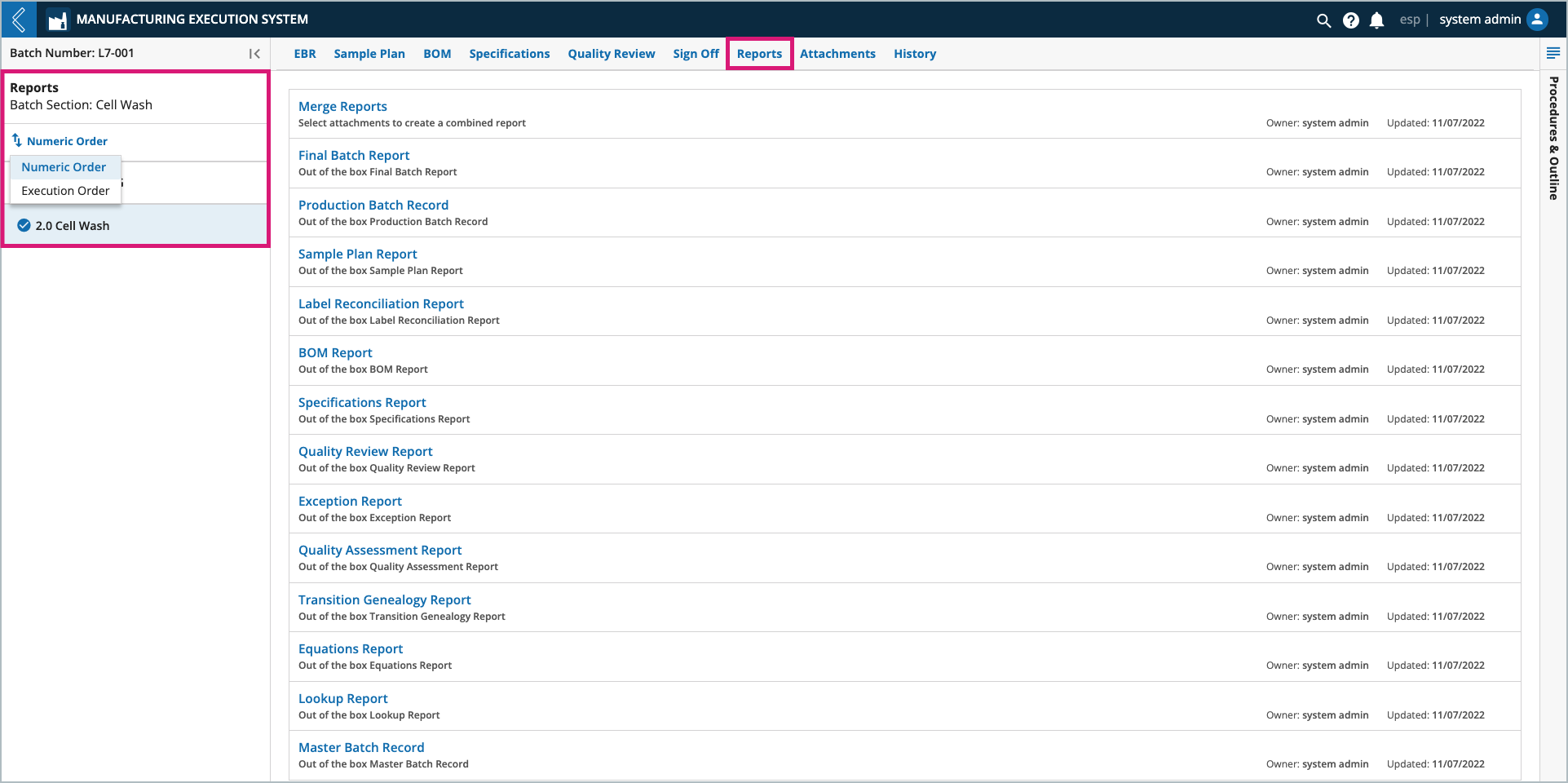
The following out-of-box reports are available from the Reports tab:
Note
The following system configurations must be in place for report generation to work. These changes can only be made when viewing this file in "code view" in L7 Configuration.
executor → api_server must be set to "http://localhost:8002",
pdf_server → allowed_urls_prefixes must include "/"
Important
Reports must be sent to Attachments to be associated with the Batch.
Final Batch Report – a record of all data collected during Batch production. This report includes:
Signatures – signatures recorded in the Sign Off tab.
EBR – all the data recorded in the Batch Record.
Sample Plan Report – the remaining reports are defined below.
Label Reconciliation Report
BOM Report
Specifications Report
Equations Report
Quality Review Report
Exception Report
Quality Assessment Report
Transition Genealogy Report
Note
Unexecuted Batch Sections in the Final Batch Report will include a "Not executed" watermark.
Reports generated for failed Batches will include a "Batch Failed" watermark on every page.
Production Batch Record – a record of all the data that will be collected during Batch production. The Production Batch Record is designed to be printed and used as a paper Batch Record, if desired. This report includes:
Signatures – table to record Sign Off signatures for the Batch.
EBR – paper Batch Record.
Sample Plan Report – the remaining reports are defined below.
Label Reconciliation Report
BOM Report
Specifications Report
Equations Report
Lookup Report
Sample Plan Report – lists all Sample IDs that were reserved, printed, and registered for the Batch based on the Sample Plan selected during Bath creation.
Note
Unused Sample IDs are not included in the Final Batch Report, but they are listed in the Production Batch Record and stand-alone Sample Plan Report.
Label Reconciliation Report – similar to the Sample Plan Report, including the destruction of unused labels.
BOM Report – lists all Items in the Batch. The Item Usage table tracks Items with quantities, whereas the Consumables Usage table tracks Items without quantities.
Specifications Report – lists all specifications for the Batch, including min and max limits, the value recorded (if saved), and an indication of exceptions.
Quality Review Report – lists all field values that were changed in the Editor Portal, including:
Old and new values
User who made the change
Time of the change
Reason for the change
Exception Report – lists all fields with a deviation or out of range exception for Steps marked as reviewed, including the Operations Reviewer, the Quality Reviewer, and their review comments.
Quality Assessment Report – lists all Exception Assessments that were entered in the Reviewer Portal, including:
Exception type
Risk level
Comment
User who performed the assessment
Time of the assessment
If the assessment was pushed to a QMS, the report also includes the time and user who performed the push, as well as the return message (as configured by the developer).
Transition Genealogy Report – lists each Batch Section and the Section that it transitioned to. This report is always sorted in execution order.
Equations Report – lists all equations used in the Batch, including the formula and the resulting value.
Lookup Report – lists all picklist or resource link (lookup) fields in the Batch. For picklists, all options are listed. For lookups, the type of object that would be presented to the user at run-time, with any filters applied, is listed.
Master Batch Record – similar to the Production Batch Record, but without Batch context. The Batch name is not included in this report, and default Sample and Specification Plans are used. This report is always sorted in numeric order.
Note
The logo in the header of L7 MES reports is configurable. The L7 logo is used by default, but a company logo or a customer-specific logo can be assigned for CDMOs.
Logo configuration is covered in more detail here.
The Merge Reports link merges individual files/reports from the Attachments tab into one (1) PDF file. For instance, you might generate a Final Batch Report, send it to Attachments, then merge it with other PDF files in the Attachments tab (i.e., instrument output files and certificates of analysis).
Note
Only PDF files in the Attachments tab can be merged using this functionality in L7 MES.
To merge reports:
Open Merge Reports in the Reports tab.
Select the PDF files you would like to merge.
The order in which the files are selected determines their order in the merged PDF. Verify the order using the Merge Order column.
Select Create. The merged report can be associated with the Batch by sending it to Attachments, downloaded, or printed like all other reports.