Planner
Goals
Understand the role of the Planner.
Know how to create Batches.
Know how to print Sample labels.
Term | Definition |
Batch | Manufacturing run to produce a Product. |
Product | The therapeutic being manufactured. |
Recipe | Manufacturing process to produce a Product. |
Specification Plan | Numeric fields with upper and/or lower limits in the Recipe. |
Sample Plan | Number and type of Samples collected in the Recipe. |
L7 MES Tab | Activity | Permission(s) |
---|---|---|
Landing Page | Create Batch | MES → Batch Creation LIMS → Workflow Chain Instance → Create |
Sample Plan | Print labels | MES → Batch Creation Analysis → Pipeline → Execute |
The Planner is responsible for creating Batches and printing Sample labels. To complete these tasks, they use the L7 MES landing page and Sample Plan tab within the Batch Record.
![]() |
The L7 MES landing page displays all Batches that have been created in L7 MES. To review or work with a Batch, select the relevant Batch Number.
Batches are listed in descending order of their creation date, and organized into three (3) tabs:
In Process – Batches that are currently active (default view).
Completed – Batches that have been completed or failed.
All – in-process and completed Batches.
All three (3) tabs display the same Batch details:
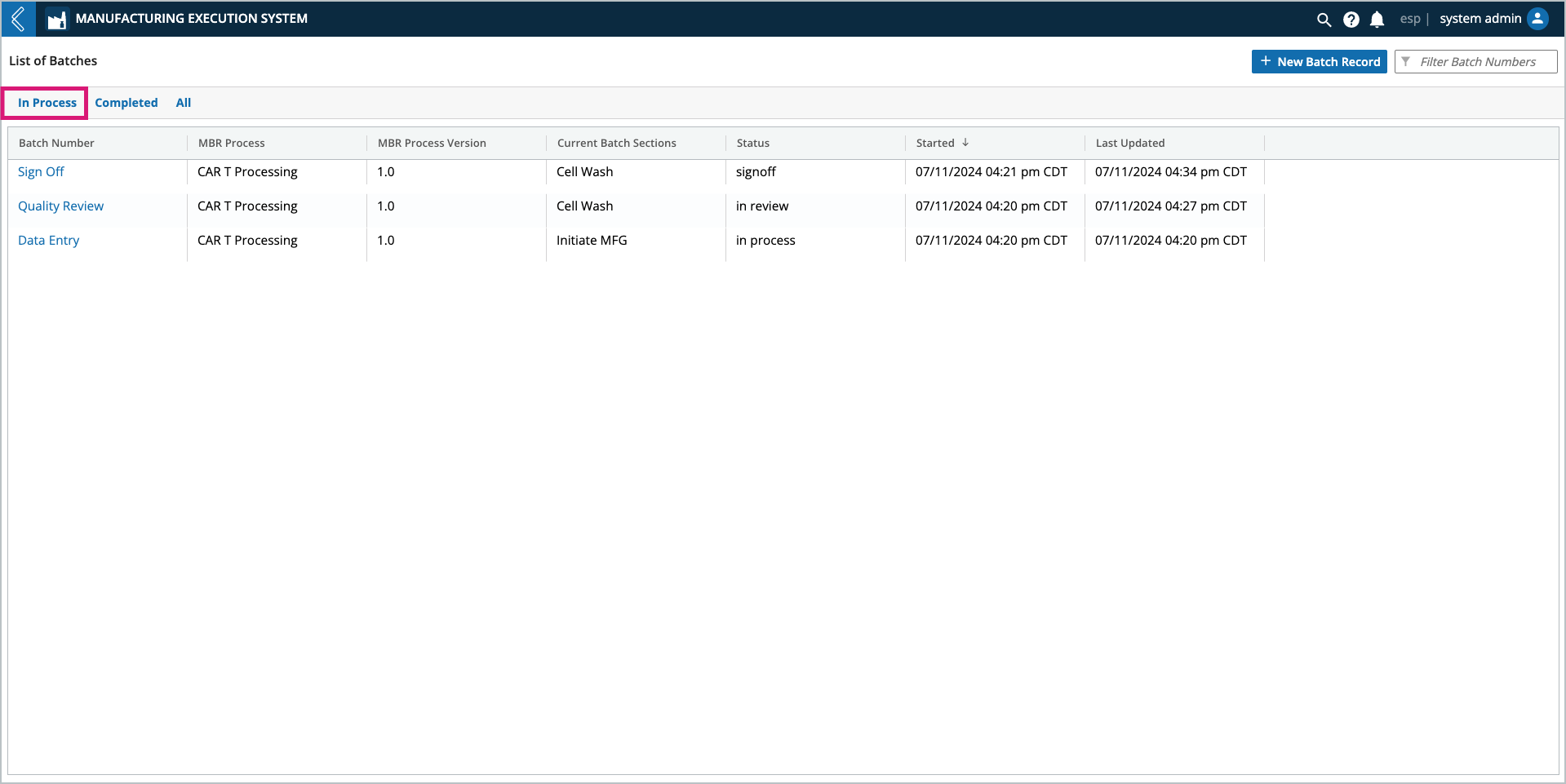
Batch Number – name of the Batch.
MBR Process – Recipe used for the Batch.
MBR Process Version – Recipe version used for the Batch.
Current Batch Sections:
If the Batch is in process, this column lists all active Batch Sections.
If the Batch is completed, this column lists the last Batch Section.
If the Batch is failed, this column lists the last Batch Section that was active at the time of failure.
Status:
In process – data is actively being collected.
In review – all Sections and Steps have been completed, but at least one Step requires review.
Reviewed – all Sections and Steps have been reviewed, and the Batch is ready for quality review signatures.
Sign-off – quality review signatures are complete, and the Batch is ready for final sign-off.
Complete – all work for the Batch is complete.
Failed – the Batch has been failed.
Started – date time the Batch was created.
Last Update – last date time any activity was recorded for the Batch.
To create a new Batch:
Go to the L7 MES landing page and select + New Batch Record.
Enter a Batch Name (free-form text).
Select which Product is being manufactured.
The Process (Recipe) is auto-populated due to its linkage with the Product.
Select which Version of the Process to use.
Select the appropriate Dynamic Execution Plan (General, Specification, Sample, BOM).
Enter any additional Batch-specific information that may be required.
Depending on how the manufacturing process has been configured, the Planner may need to enter additional information about the Batch, including Kit assignments.
Select Create.
Note
Production environments should only use pinned versions.
During Batch creation, L7 MES reserves Sample IDs so that labels can be printed for use in the Batch. These labels are typically attached to the Sample and scanned during production to complete registration.
Labels can be printed at any time during processing, but the Planner typically prints them before Batch processing begins.
To print Sample labels:
Go to the Sample Plan tab.
Select Print Labels at the top of the tab.
Select a Printer.
Select the labels to print:
All samples in the entire Batch – print one (1) label for every Sample ID reserved for the entire Batch.
All samples within a Batch Section – print one (1) label for every Sample ID reserved in the selected Batch Section.
Specific Sample Point – print one (1) label for every Sample ID reserved in the selected Sample Point.
Select Print.
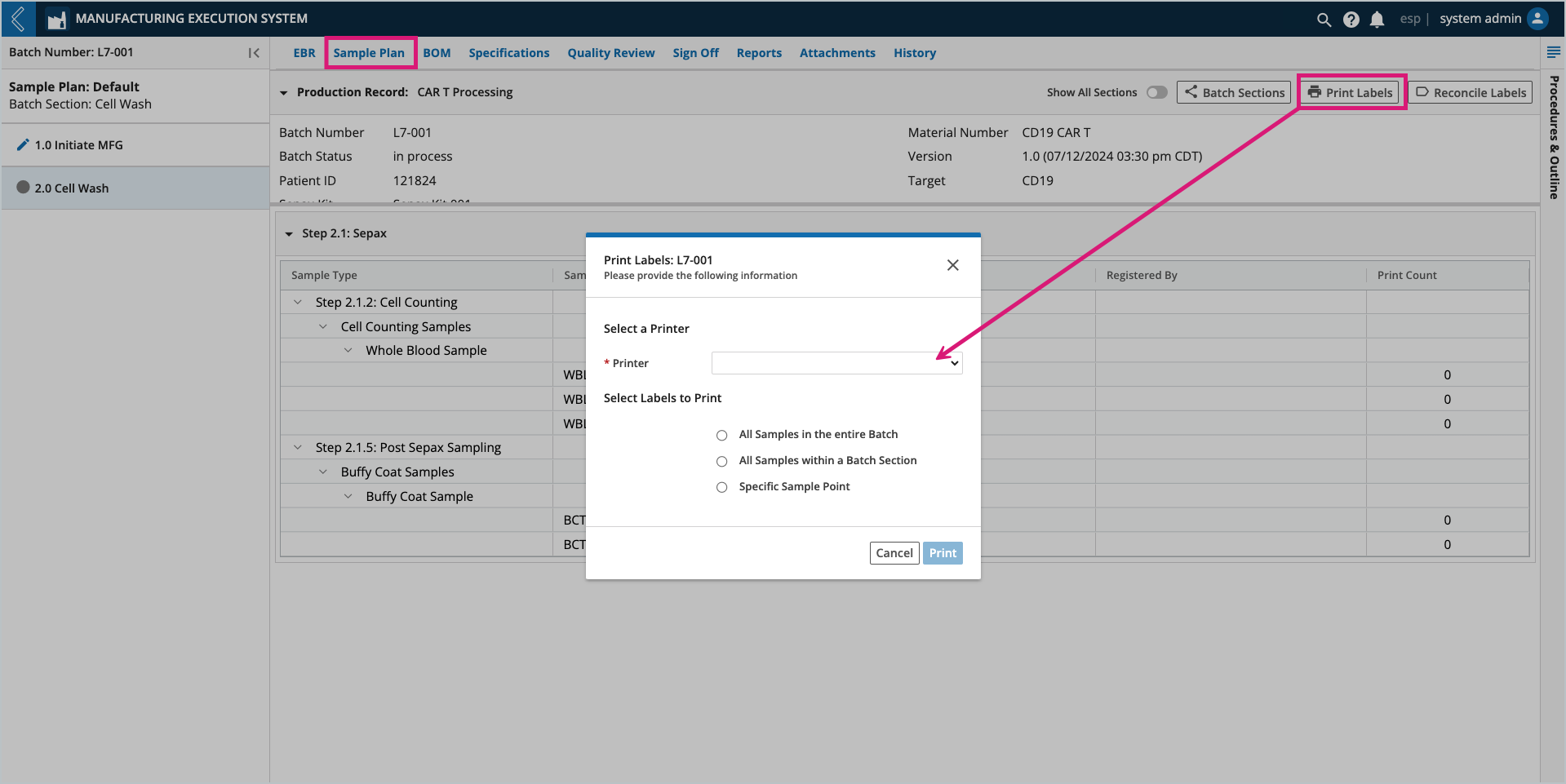
If printing is successful, the Print Count for each label is incremented.
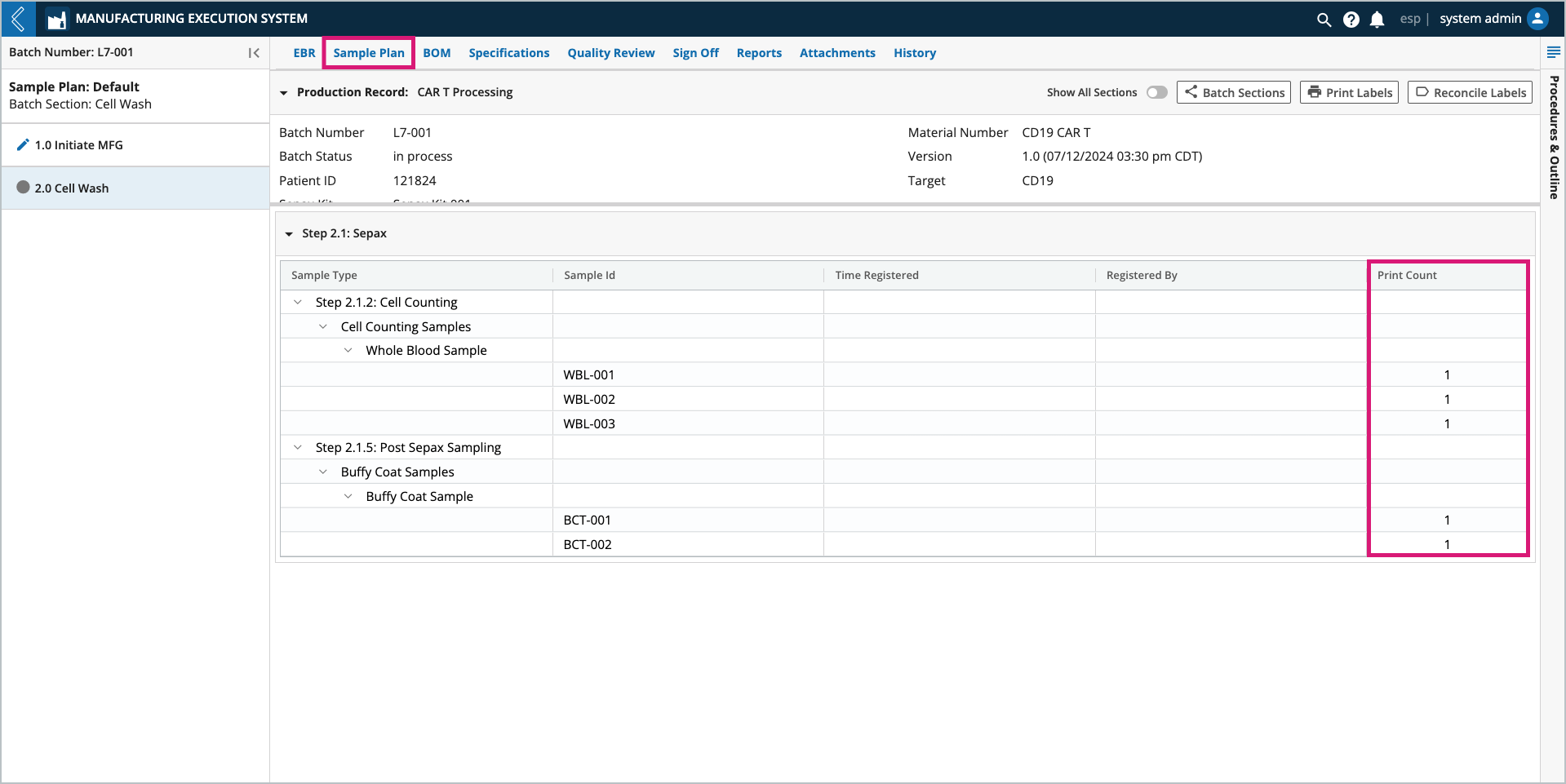